The high-throughput and precise control of matter is key for the upcoming technological revolution
Lasers enable the direct deposition of controlled amounts of materials at predefined positions on a substrate. This represents a new fabrication method, called laser additive manufacturing (AM) or 3D printing, featuring unprecedented flexibility in terms of design and functionality of the obtained structures. Laser AM can be used in a myriad of applications, including the growing field of micro-optical components.
We develop new fabrication platforms for producing functional structures at ease, high resolution and high throughput.
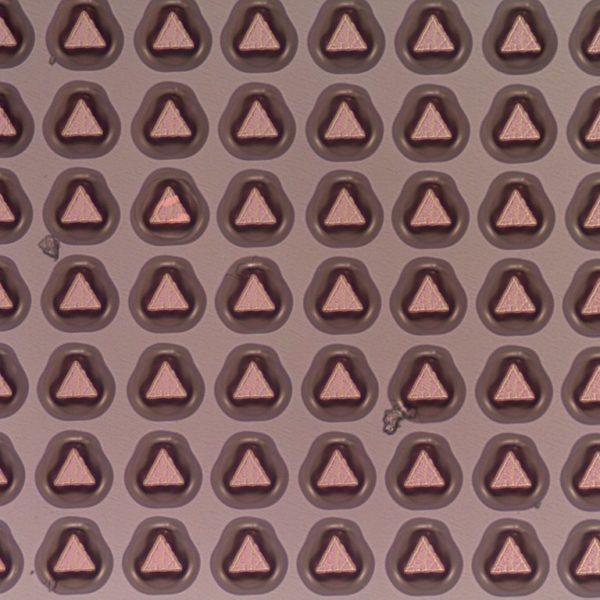
Research highlights

Laser catapulting
Laser catapulting is a single-shot laser AM method that enables the rapid fabrication of microlenses with various geometries including circular, triangular, and rectangular. It is based on a two-step process: 1- disks are “catapulted” from a thin film of a positive photoresist to a receiving substrate; 2- a thermal reflow process converts the disks into microlenses. With this method, microlens arrays with an 100% fill factor have been fabricated.

Laser-induced forward transfer
LIFT is a laser AM technique that uses lasers to transfer material from a thin film onto a substrate. An air gap between film and substrate prevents potential contamination of the latter. Notably, since LIFT does not require a nozzle as other printing technique do (inkjet printing or fused deposition modeling), it can print a wide variety of materials ranging form liquids to metals.

Overcoming the limits of traditional laser fabrication systems
We develop different strategies to overcome the current limits of laser processing regarding spatial resolution and throughput. They include: 1- using engineered materials that can be reconfigured upon exposure to an external stimulus; 2- exploiting the spontaneous formation of droplet lenses on top of a surface.